عملیات حرارتی قبل و بعد از نیتروژن دهی
قبل از نیتروژن دهی یا نیتروژن-کربن دهی به فولادها، آن ها را تحت عملیات های حرارتی آنیل نرم، نرماله، تبلور مجدد (در مواقعی که کار سرد بر روی قطعه انجام گرفته است)، تنش گیری (در مواقعی که عملیات تولیدی و ماشینکاری بر روی قطعه انجام گرفته است) و کوئنچ-تمپر (سخت کاری و برگشت) قرار می دهند. این عملیات ها به همگنی ساختار قبل از نیتریدینگ، حذف تنش های داخلی و سختی و کیفیت مناسب سطح نیتروژن دهی شده کمک می کند. فولادهای نیتروره را قبل از نیتروژن دهی، معمولاً بازپخت (آنیل) یا کوئنچ-تمپر (سخت کاری و برگشت) می کنند. این عملیات ها توسط کارخانه ی سازنده ی مقاطع فولاد نیتروره انجام می گیرد. در واقع، مصرف کننده یا کاربر، فولادهای نیتروره را در یکی از این دو وضعیت تحویل می گیرد. دمای بازپخت نرم فولادهای نیتروره معمولاً در محدوده ی ۷۲۰-۶۵۰ درجه سانتیگراد است. دمای سخت کاری آن ها نیز در محدوده ی ۹۷۰-۸۷۰ درجه سانتیگراد است. محیط سرد کردن یا کوئنچ نیز روغن یا آب است. دمای تمپر یا برگشت پس از کوئنچ آن ها نیز در حدود ۷۰۰-۵۸۰ درجه سانتیگراد است. دمای هر یک از این فرایندها برای گریدهای مختلف فولاد نیتروره در پاسخ پرسش آمده است.
فولادهای نیتروره پس از نیتروژن دهی تحت عملیات حرارتی بعدی قرار نمی گیرند. قطعات نیتروژن-کربن دهی شده را می توان تحت یک عملیات اکسیداسیون سطحی قرار داد. لایه اکسید آهن ایجاد شده به ضخامت ۱٫۵-۳ میکرون روی لایه نیتریدی می تواند خواص سایشی و مقاومت به خوردگی قطعات نیتروژن-کربن دهی شده را بهبود دهد. بهترین نتایج مقاومت به سایش زمانی به دست می آید که یک لایه ی ترکیبی با ترکیب مشخصی از فاز نیتریدی با لایه ی اکسیدی مگنتیتی به ضخامت حدود ۲ میکرون همراه شود. در صنعت عملیات اکسیداسیون پس از نیتروژن-کربن دهی را “کبود کاری” می گویند.
نیتروژن دهی موضعی
اگر فقط سخت کاری قسمت هایی از قطعه مدنظر باشد می توان با روش هایی از نیتروژن دهی به سایر نواحی جلوگیری کرد تا آن نواحی همچنان نرم باقی بمانند. برای این منظور، معمولاً از روش هایی برای پوشاندن این نواحی به منظور جلوگیری از جذب سطحی و نفوذ نیتروژن استفاده می شود. از جمله این روش ها می توان به موارد زیر اشاره کرد:
- استفاده از خمیرهای محافظ:
در نیتروژن دهی گازی و پلاسما، از خمیرهای محافظ بر پایه مس، روی، نیکل یا آلومینیوم برای پوشاندن قسمت هایی از قطعه که نباید نیتروژن دهی شوند استفاده می شود. این خمیرها باید قابل شستشو باشند تا بتوان پس از عملیات نیتروژن دهی، آن ها به راحتی از سطح قطعه پاک نمود. این خمیرها نمی توانند به طور کامل مانع از جذب سطحی نیتروژن بشوند.
- استفاده از محافظ های جرمی:
استفاده از حفاظ های جرمی مثل پیچ و مهره، پین، توپی و روکش در روش پلاسما یک روش مطمئن برای نیتروژن دهی موضعی است. چون در سطوحی که تخلیه شار الکتریکی انجام نگیرد، نیتروژن نیز به داخل قطعه نفوذ نخواهد کرد. در روش گازی به دلیل عدم آب بندی کامل، این روش زیاد قابل اطمینان نیست. در روش مایع یا حمام نمکی نیز معمولاً از این روش استفاده نمی شود.
- استفاده از پوشش های الکترولیتی:
استفاده از پوشش های الکترولیتی ضد نیتروژن دهی مثل لایه ی محافظ نیکل و مس در فرایندهای پلاسما و گازی یک روش مطمئن در مقابل نفوذ نیتروژن است. این پوشش ها ممکن است در نیتروژن-کربن دهی حمام نمکی کوتاه مدت هم به کار رود. البته استفاده از پوشش های الکترولیتی یک روش گران قیمت است.
- غوطه وری موضعی قطعه در حمام نمکی
چه فولادهایی نیتروژن دهی یا نیتروره می شوند؟
همان طور که قبلاً هم اشاره شد، بسیاری از آلیاژهای آهنی مثل چدن ها، فولادهای کربنی، فولادهای کم آلیاژ و آلیاژی، فولادهای زنگ نزن و فولادهای ابزار را می توان نیتروژن دهی نمود، ولی فولادهای نیتروره گروهی از فولادهای کربن متوسطِ دارای عناصر آلیاژی آلومینیوم، وانادیم، کروم و مولیبدن هستند که در بسیاری از کاربردهای صنعتی، نیاز به قطعات فولادی با سطح بسیار سختِ مقاوم به سایش و خوردگی و دارای استحکام خستگی مناسب به همراه مغز نرمِ چقرمه و مقاوم در برابر ضربه های وارده را پاسخ می دهند. در حضور عناصر آلیاژی با میل ترکیبی زیاد با نیتروژن در ترکیب فولادهای نیتروره، یک لایه نسبتاً نازک (تا حداکثر ۱ میلی متر) ولی سخت و پایدار نیتریدی (یا کربونیتریدی) بر روی سطح قطعه تشکیل می شود که معمولاً ۸۰۰ تا ۹۵۰ ویکرز سختی دارد. فولادهای نیتروره در فصل اول کلید فولاد معرفی شده اند. در جدول زیر، تعدادی از این فولادها معرفی شده اند.
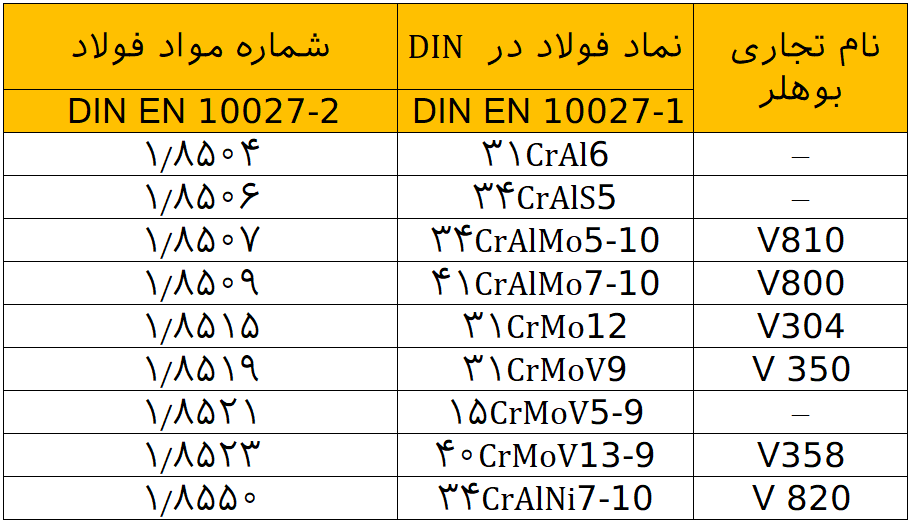
نامگذاری فولادهای نیتریده در استانداردDIN
به بخش هشتم مراجعه شود.
فروش فولادهای نیتراته
فولادهای نیتریده بدون نیتروژن دهی تحویل می شوند. مصرف کننده یا کاربر، این فولادها را معمولاً به صورت بازپخت (آنیل) نرم شده و کوئنچ-تمپر (سخت کاری و برگشت) شده تحویل می گیرد. سپس آن ها را به محصول نهایی تبدیل کرده و در نهایت نیتروژن دهی و سخت کاری سطحی می کند.
ترکیب شیمیایی فولادهای نیتروره
در جدول زیر ترکیب شیمیایی فولادهای نیتروره طبق کلید فولاد و استاندارد DIN EN 10085 آمده است:

سختی و استحکام فولادهای نیتروره قبل و بعد از عملیات سخت کاری سطحی
در جدول زیر برخی اطلاعات سختی و استحکام فولادهای نیتروره ی تحویلی به مشتری و سختی سطحی پس از نیتروژن دهی آن ها طبق کلید فولاد و استاندارد DIN EN 10084 آمده است:
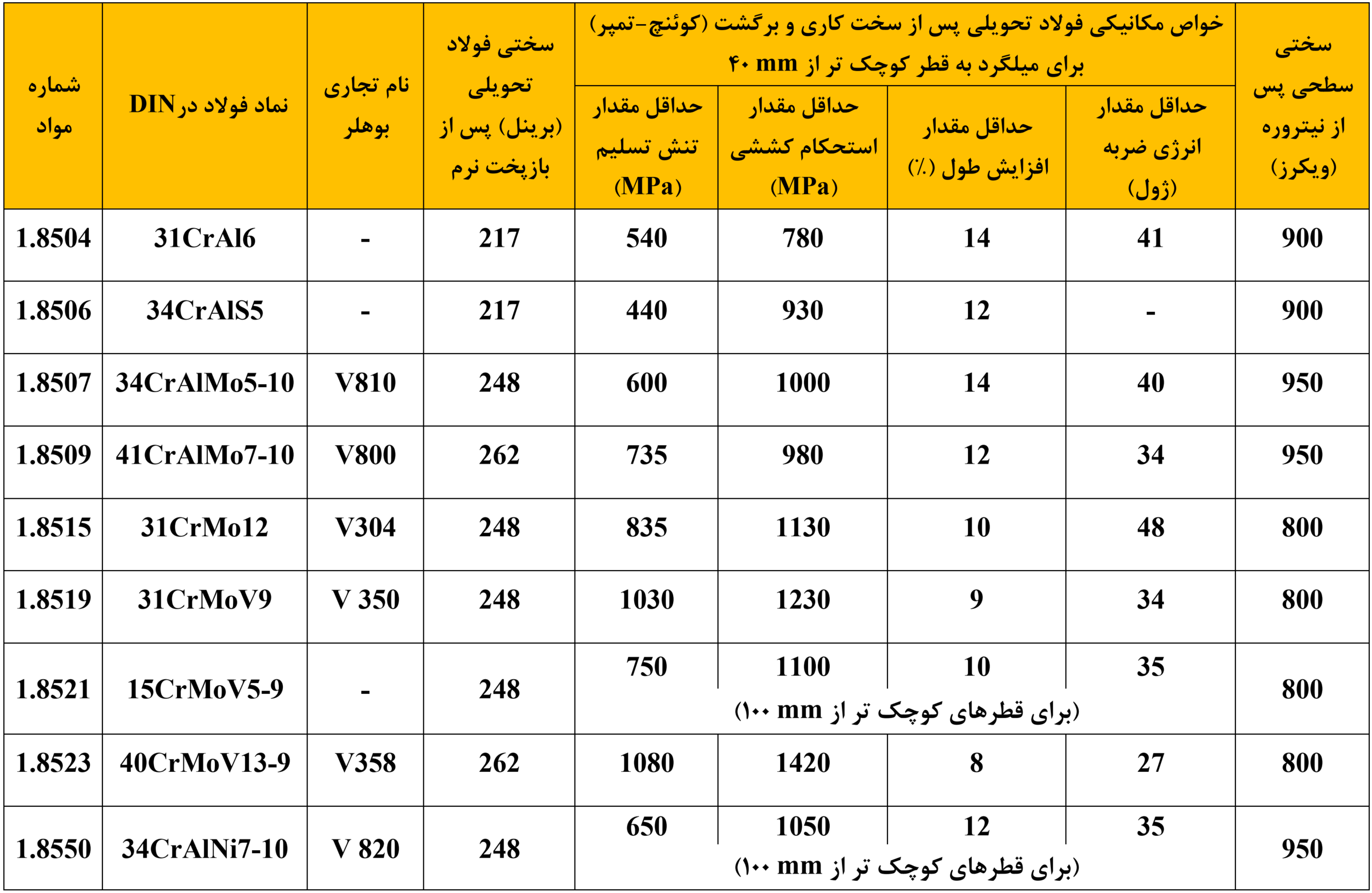
دمای نیتروژن دهی فولادهای نیتروره
در جدول زیر مشخصات نیتروژن دهی فولادهای نیتروره و عملیات حرارتی آن ها قبل از این فرایند طبق کلید فولاد و استاندارد DIN EN 10084 آمده است:
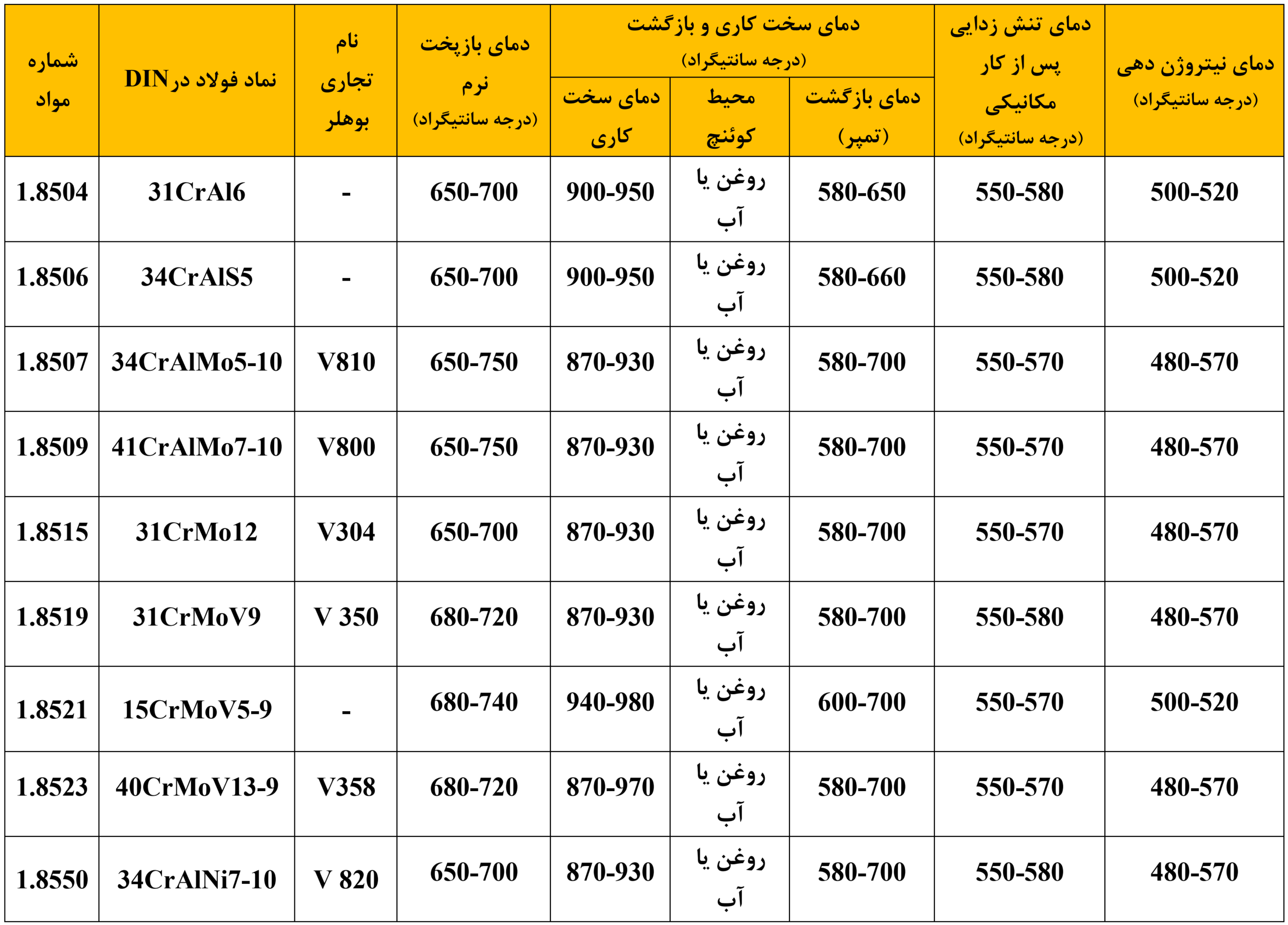