عملیات حرارتی و علت استفاده
بشر در طول سالیان طولانیِ کار با آهن و فولاد به یک نتیجه ی جالبی رسیده است و آن اینکه: با گرم و سرد کردن کنترل شده ی فولادها در حالت جامد (بدون ذوب و منجمد کردن مجدد آن)، می توان خواص کاربری قطعات، ابزار و تجهیزات فولادی را بهبود و یا تغییر داد. برای مثال، بشر در قرون قبل از میلاد توانسته بود با انجام یک سری عملیات گرم و سرد کردن بر روی شمشیرها و ادوات جنگی، از شکنندگی آن ها بکاهد.
هدف عملیات حرارتی (Heat Treatment)، دادن بهترین ویژگی های ممکن به قطعات با توجه به کاربرد آن ها است. عملیات حرارتی فولادها در حالت جامد، با تغییر ساختار میکروسکوپی یا فازی آن ها، خواص فیزیکی، شیمیایی و مکانیکی مطلوبی به فولادها می دهد و می تواند اثر بزرگ تری نسبت به تغییرات ترکیب شیمیایی در آن ها داشته باشد. در واقع، بدون تغییر ترکیب شیمیایی فولادها، می توان با عملیات حرارتی، قابلیت ها و خواص بالاتری به فولادهای پست تر (از نظر ترکیب شیمیایی) بخشید. برای مثال، با عملیات حرارتی مناسب، می توان سختی و استحکام یک فولاد کربنی را در حد یک فولاد آلیاژی افزایش داد و یا از شکنندگی یک فولاد پر کربن پیشگیری نمود.
البته ذکر این نکته خالی از لطف نیست که عملیات حرارتی نامناسب نه تنها موجب بهبود خواص نمی شود، بلکه می تواند اثر مخربی هم بر خواص و عمر قطعات داشته باشد. بنابراین حضور دو عنصر دانش متالورژیکی و تجربه ی کارگاهی، از الزامات طراحی و انجام یک سیکل عملیات حرارتی مناسب برای یک فولاد مخصوص در یک کاربری ویژه است.
چرا عملیات حرارتی باعث تغییر خواص فولادها می شود؟
دلیل تغییر خواص و ویژگی های فولادها پس از عملیات حرارتی را باید در دگرگونی و تغییر ساختار فازی آن ها جستجو کرد. اگر می خواهید پاسخ کامل تر و ملموس تری به این پرسش بلد باشید، باید یک توضیح ساده و کوتاهی در خصوص ساختار کریستالی آهن و فولاد، اثر کربن در هنگام اضافه شدن به آهن و فازها و میکروساختارهای موجود در آلیاژ آهن-کربن (فولاد) را به دقت بخوانید و یاد بگیرید.
ساختار کریستالی فلزات از کنار هم قرار گرفتن تعداد زیادی از سلول های واحد تشکیل یافته است. خود ِاین سلول های واحد از آرایش منظم و تکرار شونده ی اتم های فلزی ساخته شده اند. در ساختار بلوری آهن، دو نوع سلول واحد وجود دارد. یک سلول واحد به شکل مکعبی است که اتم های آهن در مرکز و هر گوشه ی مکعب قرار گرفته اند (شکل ۱). سلول واحد دیگر به شکل مکعبی است که اتم های آهن در مرکز هر یک از وجوه مکعب و هر گوشه ی مکعب قرار گرفته اند (شکل ۲). به سلول واحد اول، شبکه مکعبی مرکز دار (body centered cubic) یا bcc و به سلول واحد دوم، شبکه مکعبی با وجوه مرکز پر (face centered cubic) یا fcc می گویند.
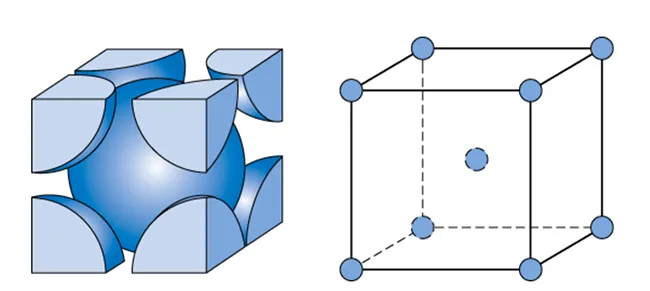
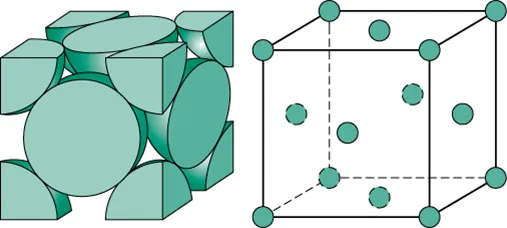
با شروع انجماد آهن در دمای ۱۵۳۸ درجه سانتیگراد، ساختار بلوری آهن جامد تا دمای حدود ۱۳۹۴ درجه سانتیگراد دارای شبکه کریستالی bcc است که به آن آهن دلتا (δ) می گویند. در این دما، ساختار آهن دچار تغییر شده و به شکل fcc در می آید که به آن آهن گاما (ϒ) می گویند. آهن گاما تا دمای حدود ۹۱۰ درجه سانتیگراد پایدار است. با عبور از این دما، ساختار کریستالی آهن باز تغییر یافته و دوباره شبکه bcc ظاهر می شود که به آن آهن آلفا (α) می گویند. آهن آلفا تا دمای محیط پایدار است. برای مشاهده ی دمای تشکیل و پایداری شبکه های بلوری مختلف آهن، نمودار تعادلی آهن – کربن (شکل ۳) را ببینید. با تغییر شبکه بلوری و نحوه ی آرایش اتم های آهن، خواص فیزیکی و مکانیکی آن نیز دچار تغییر می شود. تا اینجای مطلب را یک جای ذهن داشته باشید تا یک مطلب دیگری را بگویم.
حتماً می دانید که فولاد یک آلیاژ آهن است که از اضافه کردن کربن (از مقادیر بسیار جزئی تا ۲ درصد) به آن تشکیل می شود. کربن نقشی اساسی در فولادها دارد. حضور کربن باعث افزایش سختی، تنش تسلیم و استحکام کششی و کاهش درصد افزایش طول و مقاومت به ضربه فولادها و همچنین باعث سخت کاری یا آب دهی فولادها می شود. سوالی که اینجا مطرح است، اینست که کربن چگونه با آهن ترکیب شده و آلیاژ فولاد را به وجود می آورد؟ و با اضافه کردن کربن به آهن، چه اتفاقی در آلیاژ حاصل می افتد؟
در پاسخ به این سوال، لطفاً مطلب قبلی یعنی شبکه بلوری bcc و fcc آهن را از جایی در ذهنتان که ذخیره کرده بودید فرا بخوانید. کربن دارای چنان اتم های کوچکی است که وقتی به آهن اضافه می شود، می تواند بین اتم های آهن در شبکه های بلوری bcc و fcc قرار بگیرد و تشکیل یک محلول جامد را بدهد. محلول جامد فازی است که در آن اتم های یکی از عناصر آلیاژی می تواند در شبکه بلوری عنصر اصلی به صورت جانشینی (جایگزین یکی از اتم های عنصر اصلی) یا بین نشینی (در میان اتم های عنصر اصلی) قرار بگیرد. از آنجایی که آهن دارای سه نوع حالت کریستالی (آهن آلفا، گاما و دلتا) است، با قرارگیری کربن در بین اتم های این سه نوع آهن، سه نوع فاز (محلول جامد) در فولادهای ساده کربنی به وجود می آید که عبارتند از:
- فاز فریت (Ferrite) آلفا: محلول جامد بین نشین کربن در آهن آلفا با شبکه bcc (شکل ۴).
- فاز آستنیت (Austenite): محلول جامد بین نشین کربن در آهن گاما با شبکه fcc
- فاز فریت دلتا: محلول جامد بین نشین کربن در آهن دلتا با شبکه bcc
ناحیه ی تشکیل و حضور این فازها در فولاد ساده کربنی یا آلیاژ آهن-کربن را در دیاگرام زیر که به دیاگرام تعادلی آهن – کربن مشهور است، می توانید ببینید. میزان حلالیت یا درصد کربن بین نشین در هر یک از انواع آهن ها متفاوت است. در دیاگرام آهن-کربن، حداکثر میزان حلالیت کربن در آهن آلفا، گاما و دلتا به ترتیب ۰٫۰۲، ۲٫۱۱ و ۰٫۱ درصد نشان داده شده است. با توجه به دمای پایداری فریت دلتا (بیش از ۱۳۹۴ درجه سانتیگراد)، این فاز اهمیتی در بحث عملیات حرارتی ندارد، لذا منظور از فریت در مباحث بعدی، فریت آلفا است. از آنجایی که بیشتر فولادها دارای عناصر آلیاژی به جز آهن و کربن هستند و این عناصر موقعیت مرز بین نواحی مختلف فازی و دما و گستره ی پایداری آن ها را نسبت به فولادهای ساده کربنی تغییر می دهند، دیاگرام آهن – کربن تنها به عنوان یک راهنمای عمومی استفاده می شود و کاربرد تخصصی در مطالعه ی فازی و عملیات حرارتی انواع فولادها را ندارد.
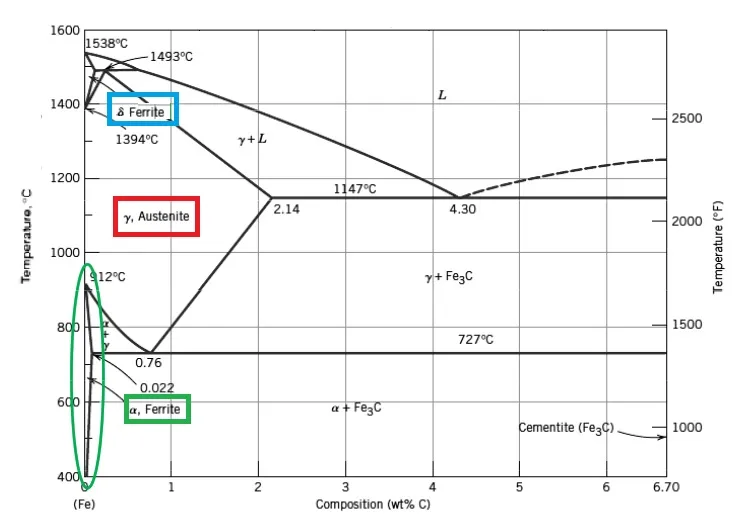
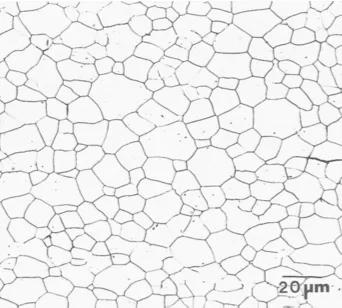
همان طور که در بند بالا اشاره شد، حلالیت کربن در آهن محدود است. پس شاید این سوال پیش بیاید که چه بر سر کربن اضافی در ترکیب آلیاژ یا کربنی که نتوانسته در تشکیل محلول جامد بین نشینی کربن در آهن (فریت و آستنیت) شرکت کند، می آید؟
پاسخ اینست که این کربن اضافی به دو صورت دیگر می تواند در آلیاژ آهن – کربن ظاهر شود:
۱- سمنتیت (Cementite) یا کاربید آهن (Iron Carbide): ترکیب بین فلزی سه اتم آهن و یک اتم کربن با فرمول Fe3C است که مقدار درصد کربن در آن، ۶٫۶۷ درصد است. شبکه بلوری سمنتیت از نوع bcc و fcc نیست، بلکه از نوعی شبکه بلوری دیگر به نام اورترومبیک است. سمنتیت یک فاز بسیار سخت و ترکیبی ناپایدار است.
۲- گرافیت (Graphite): اگر درصد کربن زیاد و سرعت سرد شدن آهسته باشد، کربن به صورت آزاد در ساختار باقی می ماند که به آن گرافیت می گویند. گرافیت در چدن ها (آلیاژهای آهن – کربن با بیشتر از ۲ درصد کربن) دیده می شود. ناپایداری سمنتیت باعث می شود که تحت شرایط خاص تجزیه شده و کربن آزاد یا گرافیت تولید کند.
با این توضیحات، تاکنون مشخص شده است که ساختار آلیاژهای فولاد کربنی در دمای محیط می تواند از محلول های جامد فریت و آستنیت و ترکیب بین فلزی سمنتیت یا کاربید آهن تشکیل شده باشد. علاوه بر این فازها، ساختارهای دیگری هم در فولادها دیده می شود که به صورت هیچ کدام از فازهای قبلی (محلول جامد بین نشین یا ترکیب بین فلزی) نیستند، بلکه از دگرگونی یا تغییر ساختار آستنیت به هنگام سرد شدن فولاد در عبور از دمای حدود ۷۲۷ درجه سانتیگراد (خط A1 در دیاگرام آهن – کربن) به وجود می آیند. این فازها عبارتند از:
پرلیت (Pearlite):
پرلیت مخلوطی از لایه های متناوب دو فاز فریت و سمنتیت است که از دگرگونی آستنیت در هنگام سرد شدن آهسته و تحت مکانیسم نفوذ اتمی (جوانه زنی و رشد) به وجود می آید. شکل ظاهری پرلیت مشابه اثر انگشت بر روی کاغذ است.
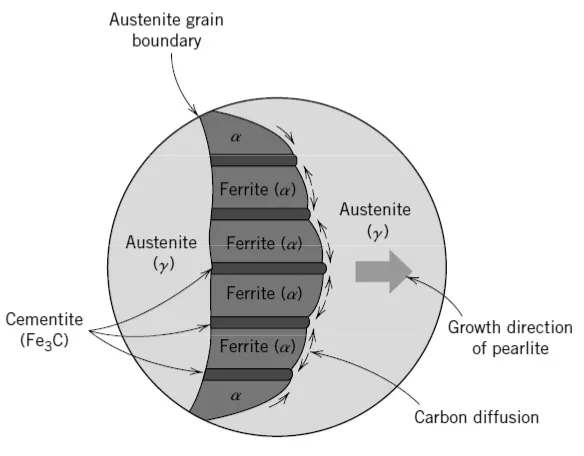
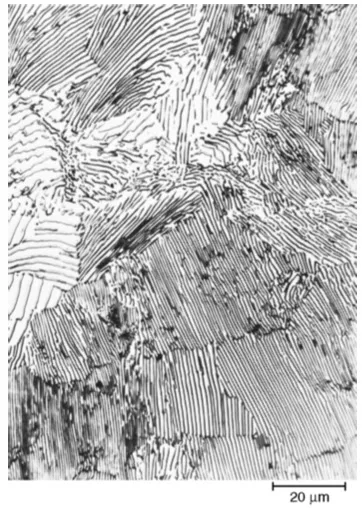
مارتنزیت (Martensite):
مارتنزیت یک فاز غیر تعادلی سخت است که از سریع سرد کردن آستنیت و طی یک استحاله غیر نفوذی تشکیل می شود. با تشکیل مارتنزیت، کربن محلول در شبکه bcc به مقدار زیادی افزایش یافته و جاهای خالی بیشتری از شبکه توسط کربن اشغال می شود. در نتیجه، شبکه بلوری از bcc مکعبی به bct مکعب مستطیلی تغییر می یابد.
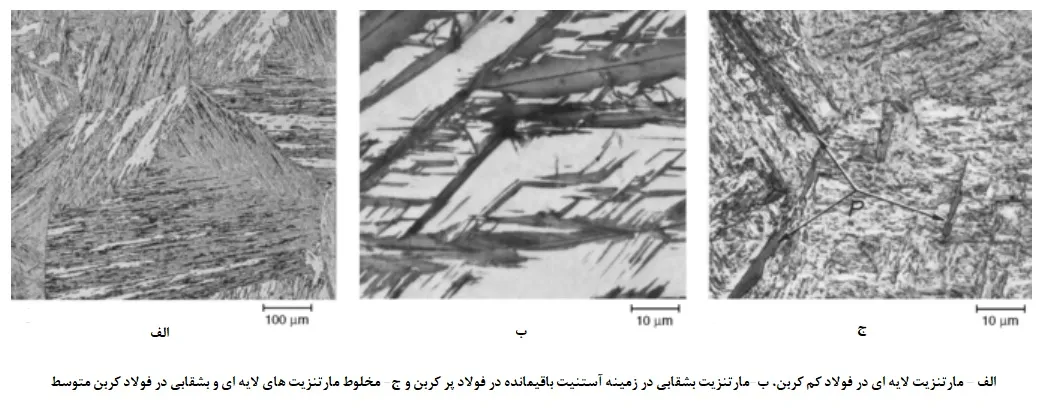
بینیت (Bainite):
بینیت یک فاز غیر تعادلی سخت است که از سریع سرد کردن آستنیت (مثل مارتنزیت) ولی طی یک استحاله نفوذی (مثل پرلیت) تشکیل می شود. بینیت مثل پرلیت مخلوطی از فازهای فریت و سمنتیت است، با این تفاوت که فریت و سمنتیت به صورت لایه های متناوب کنار هم قرار نگرفته اند، بلکه در این ساختار، صفحات فریتی، ذرات سمنتیتی را در بر گرفته اند (بینیت پایینی) یا اینکه ذرات سمنتیت در فصل مشترک فریت – آستنیت و بین صفحات فریتی جوانه زده و رشد می کند (بینیت بالایی). بینیت مثل مارتنزیت به صورت سوزنی شکل دیده می شود
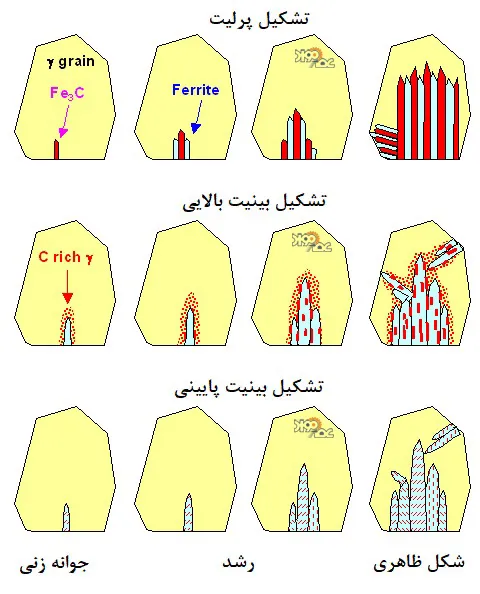
جمع بندی
وقتی در پروسه ی تولید، فولاد از دمای مذاب تا دمای اتاق سرد می شود، میکروساختار فازی آن ممکن است شامل فازهایی چون فریت، پرلیت، سمنتیت، مارتنزیت، بینیت و یا آستنیت باقیمانده (آستنیت تبدیل نشده به سایر فازها) باشد. هر یک از این فازها، خواص ویژه ای به فولاد می بخشد. برای مثال، فریت یک فاز نرم ولی انعطاف پذیر ولی مارتنزیت یک فاز سخت و شکننده است. عملیات حرارتی به این منظور انجام می شود که ساختار فازی را متناسب با کاربری و انتظاری که از قطعه یا ابزار فولادی داریم، تغییر دهد. نتیجه ی این تغییر، بهبود خواص فیزیکی، شیمیایی، مکانیکی و تکنولوژیکی فولاد و برآورده شدن انتظارات کاربر است. عملیات حرارتی این اجازه را به ما می دهد که در صورت امکان بتوانیم ساختار فولاد را به ساختار دلخواه خود برای کاربری مورد نظر تغییر دهیم. مثلاً میکروساختار را به مارتنزیت تبدیل کنیم تا سختی و استحکام قطعه افزایش یابد یا میکروساختار را به پرلیت یا فریت و یا مخلوطی از آن ها تبدیل کنیم تا سختی کاهش یابد و ماشین کاری قطعه با سهولت انجام بگیرد و یا حتی با عملیات حرارتی می توانیم دانه بندی پرلیت را ریزتر و ظریف تر کرده و سختی و استحکام قطعه را افزایش دهیم.
برای اینکه تغییر ساختار فازی فولاد در عملیات حرارتی قطعه اتفاق بیفتد، آن را تا یک ناحیه ی دمایی مشخص گرم و سپس تا دمای محیط سرد می کنند. به این صورت که، ابتدا با گرم کردن، ساختار فولاد را معمولاً به تک فاز آستنیت تبدیل می کنند. آستنیت این قابلیت را دارد که در ضمن سرد شدن فولاد به فازهای مختلفی تبدیل شود. لذا با سرد کردن فولاد از ناحیه ی پایداری آستنیت، ساختار آن را به فازهای مطلوب (مثل پرلیت، فریت، مارتنزیت، بینیت یا مخلوطی از آن ها) تبدیل می کنند. سرعت سرد شدن فولاد از ناحیه ی آستنیتی مهم ترین تاثیر را بر ساختار فاز نهایی دارد. برای کنترل سرعت سرد شدن نیز از محیط های مختلف سرد کردن مثل داخل کوره، هوای محیط، آب، روغن، نمک های مذاب و غیره استفاده می کنند.