تقسیم بندی انواع روانکار ها
مقدمه
روانکارها را در یک نگاه کلی میتوان به دو دسته بزرگ روانکارهای خودرو و روانکارهای صنعتی تقسیم .کرد روانکارهای صنعتی نیز به دو دسته عمده روغنهای صنعتی و روانکارهای مخصوص دیگر مثل گریسها روانکارهای فلزکاری و روانکارهای جامد تقسیم میشوند.
البته میتوان روانکارها را از نظر نوع حالت فیزیکی نیز طبقه بندی کرد روانکارها از نظر حالت به چهار دسته روان کننده های گازی روان کننده های مایع گریسها و روان کننده های جامد تقسیم میشوند .
روانکارهای گازی
روانکارهای گازی مثل ،هوا هلیوم، بخار مایعات و … در درجه حرارتهای خیلی بالا و یا ،پایین سرعت بسیار زیاد و بارکم و یا در مواردی که پرتوهای هسته ای در محیط وجود دارند استفاده میشوند یکی از خصوصیات بسیار مهم روانکارهای گازی این است که گرانروی آنها با تغییر درجه حرارت تغییر چندانی نمیکند به همین دلیل این روانکارها قادرند در گستره وسیعی از کاربردهای صنعتی مورد استفاده قرار گیرند علاوه بر این گازها سبک تر از مایعات هستند و میتوان وزن آنها را نادیده گرفت. این موضوع باعث میشود در سرعتهای خیلی ،بالا همچنان جریان گازها آرام و یکنواخت باقی بماند به همین جهت کارکرد روانکارهای گازی در یاتاقانهای با سرعت خیلی زیاد بهتر از روانکارهای مایع است. روانکارهای گازی اصطکاک درونی کمی دارند عاری از ناخالصی اند و خاصیت سرریزی که در مورد روانکارهای مایع و گریس ها پیش می آید را ندارند. علاوه بر آن این نوع روانکارها به دلیل سرریز نکردن میتوانند مواد مطمئنی در صنایع غذایی داروئی و شیمیایی نیز باشند روانکاری اولتراسانتریفیوژها، ماشین ابزار سنگزنی دقیق که با سرعت زیاد کار میکنند، چرخ مته دندانپزشکی، راکتورهای اتمی، ماشینهای ریسندگی پرسرعت، توربینهای گازی موتور جت و … از جمله موارد کاربرد این دسته از روانکارها هستند.
روانکارهای مایع
روغنها مهمترین روانکارهای مایع هستند که خود به دو دسته ی بزرگ روغنهای معدنی و روغنهای سنتزی تقسیم بندی میشوند. این نوع روانکارها رایج ترین و پرمصرفترین نوع روانکارها هستند. هر دو دسته به نوعی از مشتقات نفت خام به حساب می آیند با این تفاوت که روغنهای معدنی از انجام یک سری عملیات تفکیک بر روی نفت خام و حداکثر یک واکنش شیمیایی کنترل شده به دست میآیند در صورتیکه برای تولید روغنهای سنتزی واکنشهای شیمیایی کنترل شده بیشتری مورد نیاز است و به همین دلیل قیمت تمام شده روغنهای سنتزی بیشتر از روغنهای معدنی خواهد بود. به طور کلی روغنهای معدنی به دلیل کاربرد فراوانی که در تولید روانکارها دارند نسبت به روغنهای سنتزی بیشتر تولید میشوند. البته قابلیتهای یک روغن سنتزی به دلیل واکنشهای مخصوصی که روی آن انجام شده بیشتر از یک روغن معدنی است.
البته به جز روغنهای سنتزی و روغنهایی که منبع اصلی آنها نفت خام است روغنهای دیگری نیز وجود دارند که از جانوران ماهیها و گیاهان به دست میآیند که روغنهای طبیعی نام دارند. استفاده از این روغنها به عنوان روانکار در گذشته بسیار مرسوم بوده است ولی امروزه نفت خام منبع اصلی تولید روانکارها است. یکی از خصوصیات روغنهای طبیعی تجزیه بیولوژیکی و زیست تخریب پذیری آسان آنها است که از این لحاظ نسبت به روغنهای پایه معدنی و سنتزی برتری دارند. این روغنها برای مدت طولانی قابل نگهداری نیستند ضمن اینکه هزینه ی تولید زیادی هم دارند اما با توجه به محدود بودن منابع نفتی برای تولید انرژی، روغنهای طبیعی میتوانند جایگزین مناسبی برای مشتقات نفتی در عرصه تولید روانکار باشند.
گریس ها
گریس ها جزو معروفترین روانکارها هستند که نه مایع و نه جامدند. گریس ها از یک روغن پایهی معدنی یا سنتزی و یک پرکننده یا سفت کننده به دست می آیند. در مواردی که انجام روانکاری با روانکارهای مایع مشکل است، روانکاری مجدد محل مورد نظر محدودیت دارد و یا اینکه یکبار روانکاری برای مدت زمان طولانی کفایت میکند این نوع روانکارها کاربرد فراوانی خواهند داشت.
روانکارهای جامد
این نوع روانکارها برای کار در شرایط بخصوص مثل خلاء، بار زیاد و یا حرارت بالا و کاربردهایی مثل راکتورهای هسته ای که روانکار در برابر اشعه های رادیواکتیو قرار دارد، استفاده میشوند پایداری در برابر خلا، فراریت کم در درجه حرارتهای بالا و همچنین مقاومت در برابر انرژی ناشی از تابشهای رادیواکتیو از مهمترین خواص یک روانکار جامد است. گرافیت، مولیبدنیوم دی سولفید، بورنیترید، تنگستن دی سولفید و برخی ترکیبات آلی جامد مثل فتالوسیانین و تترا فلوئورواتیلن، میکا، تالک و … از انواع روانکارهای جامد هستند. در این بین گرافیت و مولیبدنیوم دی سولفید بیشترین کاربرد را دارند.
انواع لایه های روانکاری
مقدمه
به طور کلی لایه های روانکاری به سه دسته عمده تقسیم میشوند:
1- لایه های نازک (لایه های سیال نازک)
2- لایه های سیال
3- لایه های جامد
لایه های سیال ،خود شامل لایه های هیدرودینامیک ضخیم هیدرواستاتیک ضخیم ،الاستوهیدرودینامیک و لایه های فشرده میباشند.
لایه های نازک
برای ثابت نگه داشتن لایه روانکار لازم است که یک جریان پیوسته ی روانکار همیشه وجود داشته باشد. در خیلی از حالات این امر عملی نیست و یا ممکن است فشار وارده بر سطوح به قدری زیاد یا سرعت حرکت به قدری کم باشد که تشکیل فیلم سیال ممکن نباشد تحت این شرایط لایه های روانکاری، لایه های نازک نامیده میشوند.
لایه های هیدرودینامیک ضخیم
در این حالت ضخامت لایهی روغن چندین برابر مجموعه ناصافی های سطوح متحرک روی هم میباشد و فشار هیدرولیکی لایه ی روغن چنان است که در مجموع با نیروی وارده بر سطوح متکی بر یکدیگر برابری و مقابله میکند این نوع لایه ی روانکار به علت سرعت نسبی سطوح روانکاری شده و شکل هندسی مناسب آنها ایجاد میشوند. لایه های هیدرواستاتیک ضخیم لایه های هیدرواستاتیک ضخیم به وسیله ی پمپ شدن سیال با فشار بالا بین سطوحی که ممکن است نسبت به یکدیگر متحرک یا ثابت باشند، تشکیل میشوند. در این حالت فشار روغن به حدی است که میتواند جسم فوقانی را به صورت شناور روی فیلم سیال نگه دارد.
لایه های فشرده
وقتی که سطوح تماس در اثر فشار به یکدیگر نزدیک میشوند، بر لایه ای از روغن که بین آنها قرار گرفته فشار زیادی وارد میشود. با افزایش فشار گرانروی نیز افزایش یافته و در نتیجه روغن نمیتواند با سرعت از بین سطوح تماس خارج شود بنابراین لایه ی روغن متراکم شده و میتواند بار زیادی را برای مدتی کوتاه تحمل کند؛ به این حالت لایه فشرده میگویند. البته اگر افزایش فشار تداوم یابد بالاخره روغن از بین سطوح خارج شده و تماس فلز با فلز رخ خواهد داد.
انواع رژیمهای روانکاری
مقدمه
در سامانه های روانکاری بسته به شرایط مختلف از رژیم های روانکاری متفاوتی استفاده میشود.
روانکاری هیدرودینمامیک
در این رژیم روانکاری هیچ نوع تماس سطح به سطح وجود نداشته و گرانروی روغن به اندازه ای است که میتواند شفت و یاتاقان را از یکدیگر جدا نگه دارد. در این رژیم روانکاری، تنها اصطکاک موجود، اصطکاک داخلی روغن است. یک لایه روغن یک قطعهی گردنده مانند میل لنگ را به صورت شناور نگه داشته و از تماس آن با یاتاقان جلوگیری می کند. در روانکاری هیدرودینامیک حرکت دو سطح نسبت به هم همگراست و روغن به داخل سطح کشیده میشود. در واقع روغن کاری هنگامی شروع میشود که ماشین روشن شده و سرعت و بار در آن به حدی رسیده که شرایط لازم برای کشیده شدن یک لایه ی روغن بین شفت و یاتاقان به وجود آید. در ماشین هایی که دارای شفت دوران کننده در داخل یاتاقان هستند این نوع روانکاری صورت میگیرد. در روانکاری هیدرودینامیک خواص فیزیکی روغن و به خصوص گرانروی آن باید ثابت بماند زیرا کاهش بیش از حد گرانروی باعث تماس مستقیم فلز به فلز میشود. همچنین افزایش بیش از حد گرانروی به دلیل مقاومت داخلی زیاد روغن باعث کاهش بازده ماشین میشود.
روانکاری الاستوهیدرودینامیک
وقتی فشارهای تماسی بالا در سیستم وجود داشته باشد به روانکاری الاستوهیدرودینامیک نیاز خواهد بود؛ همچنان که روان کننده به سطح تماس کشیده میشود فشار روی آن بالا رفته و در نتیجه گرانروی آن نیز بالا می رود. گرانروی بالا و کوتاه بودن زمان مورد نیاز برای روانکاری باعث میشود که روان کننده نتواند از بین سطوح فرار کند و در نتیجه باعث جداماندن سطوح از یکدیگر میشود. تا زمانیکه شرایط عملکرد مانند سرعت، بار و دما خیلی زیاد نشود به دلیل لایه ی ایجاد شده تماس سطح به سطح رخ نمیدهد. برای مثال وقتی روغن در منطقهی تماس بین ساچمه و مسیر حرکت قرار میگیرد فشار آن به شدت افزایش مییابد این افزایش فشار باعث افزایش گرانروی روغن و همین طور تغییر حالت آن به صورت نیمه جامد یا پلاستیکی خواهد شد بعد از کم شدن فشار روغن به حالت اول خود بر میگردد.
لایه های EHL (Elasto-Hydrodynamic Lubrication) لایه های بسیار نازکی هستند که هرچه سرعت زیاد شود، ضخامت لایه نیز بیشتر خواهد شد؛ گرانروی افزایش، بار کاهش و انطباق هندسی سطوح تماس بهبود می یابد. ضخامت لایه ی روان کننده خیلی به میزان بار بستگی ندارد زیرا لایهی روغن در فشار موجود در سطوح تماس، سفت تر از سطوح فلز است. ارتباط بین ناهمواریهای سطوح و ضخامت لایه در روانکاری الاستوهیدرودینامیک مهم است. این رژیم روانکاری معمولاً در عملیات فلزکاری مخصوصاً در فلزکاری غلتشی و کششی دیده میشود. گاهی اوقات عامل انتقال نیرو در این روانکاری عنصر غلتانی مانند غلتک یا ساچمه بین دو سطح یاتاقان است و به همین خاطر آنرا روانکاری غلتان نیز مینامند. تشکیل لایه های الاستوهیدرودینامیک در یاتاقانها همیشه با افزایش درجه حرارت همراه است. اگر این افزایش باعث کاهش بیش از حد گرانروی روغن شود به سیستم صدمه ی جدی وارد میشود.
روانکاری جامد
در بعضی سیستمهای روانکاری باید از روان کننده هایی استفاده کرد که یک لایه ی دائمی و پایدار با سطح تشکیل دهند. مثلاً در سیستمهایی که نتوان از روغن یا گریس به هر دلیلی استفاده کرد، این نوع روانکاری مورد استفاده قرار میگیرد در این نوع سیستمها، اغلب تماس دو سطح با یکدیگر یا کامل (یاتاقان،کشویی کف گرد و …) یا خطی (از طریق کاردک) و یا نقطه ای (یاتاقانهای سوزنی) است. برای روانکاری جامد از مواد خود روانکار استفاده میکنیم. برخی مواد به دلیل ناهمگونی در خواص مکانیکی و مثلاً به دلیل تغییر ساختاری که در اثر تنش برشی کم در ساختمانشان رخ میدهد یک ضریب اصطکاک کوچک در لایه هایشان به وجود میآید. این ناهمگونی در خواص مکانیکی و یا به عبارت ساده تر صفحات جسم مشخصه اجسام لایه ای میباشد. اگر این لایه ها در جسمی بتوانند بر اثر نیروی برشی کم بر روی هم بلغزند، جسم مورد نظر خودروانکار نام دارد که در روانکاری جامد از آن استفاده میشود. برای نمونه گرافیت یک ماده ی خودروانکار است و به طور گسترده از آن در روانکاری جامد استفاده میشود. به طور کلی مواد خودروانکار باید شامل سه ویژگی زیر باشند.
– ساختار لایه ای داشته باشند
– توانایی چسبیدن به سطوح و ایجاد لایه روی آن را داشته باشند.
– دچار هیچ گونه تجزیه و یا واکنش شیمیایی در دمای عملکرد محیط مورد نظر نشوند.
روانکاری مرزی
در این سیستم روانکاری بیشترین مقدار اصطکاک رخ میدهد. کم بودن روغن سرعت بسیار کم سطوح و یا زیاد بودن بار باعث میشود که لایه ی بسیار نازکی از روانکار(در حد ابعاد مولکولی) تمامی نیروی وارده را تحمل کند. این حالت در هنگام روشن کردن ماشین آلات در سرعتهای کم و یا بار زیاد ایجاد میشود. در چنین وضعیتی روان کننده دارای نقش بسیار کم و یا حتی بدون نقش است بهترین کار برای جلوگیری از سایش در این حالت استفاده از روغنهایی است که دارای مواد افزودنی فشار پذیر یا ضدسایش باشند. این مواد با سطوح واکنش میدهند و یک لایه ی محافظ بر روی آنها ایجاد میکنند و به جای سطوح فلزی ساییده میشوند.
افزایش جریان و گرانروی روغن نیز میتواند به جلوگیری از سایش قطعات کمک کند ولی افزایش گرانروی سبب افزایش اصطکاک داخلی میشود و دمای روانکار را بالا میبرد که در نهایت ممکن است از مقاومت روانکار بکاهد. به طور کلی برای درک رژیمهای روانکاری در نظر داشتن ضخامت لایه ی روانکاری که بین دو سطح در یک سیستم تریبولوژی شکل میگیرد از اهمیت زیادی برخوردار است. تشخیص نوع رژیم روانکاری در بیشتر کارهای عملی فلزکاری به آسانی امکان پذیر نیست و نمیتوان به راحتی میزان ضریب اصطکاک در تماسهای مختلف را اندازه گیری کرد.
رژیم های روانکاری برحسب ضخامت لایه ی روانکار به ۴ دسته ی کلی تقسیم میشوند لایهی نازک، لایه ی ضخیم، لایه ی مخلوط و لایه ی مرزی. وقتی که سطوح تحت شرایط لایه نازک روی یکدیگر حرکت کنند اغلب سیال به اندازه کافی وجود دارد که مقداری از بار بتواند به وسیله لایه ی نازک سیال و قسمت دیگر به وسیله تماس بین سطوح حمل شود. این شرایط را اغلب روانکاری لایه مخلوط میگویند. در روانکاری لایه مخلوط ممکن است در بعضی قسمتهای سطوح فیلم سیال و در بعضی قسمتهای دیگر فیلم نازک مشاهده شود. در شکل های زیر انواع رژیمهای روانکاری و ضخامت لایههای روانکار موجود در آنها آمده است.
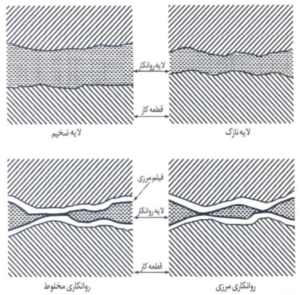
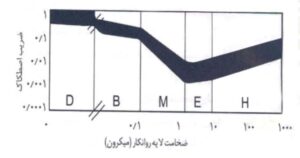